Currently, most PCB manufacturing processes use the subtractive method, where excess copper foil is removed from the raw copper-clad laminate to form conductive patterns.
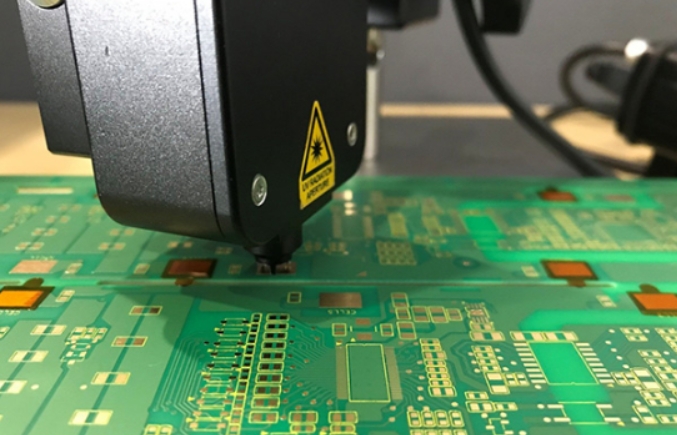
Manufacturing Process of Multilayer PCBs
The subtractive method primarily employs chemical etching, which is both economical and efficient. However, since chemical etching attacks indiscriminately, the desired conductive patterns must be protected by applying a layer of resist. The unprotected copper foil is then etched away. Early resists were applied using screen printing, where resist ink was printed in the form of circuits, hence the term “printed circuit board (PCB).” However, as electronic products became more precise, the resolution of printed circuits could no longer meet product requirements. This led to the adoption of photoresists as the material for image resolution. Photoresist is a photosensitive material that reacts to light of a specific wavelength, forming a polymer through a photochemical reaction. By selectively exposing the photoresist using a patterned film and then developing it (e.g., with a 1% sodium carbonate solution), the unexposed photoresist is removed, leaving behind the protective pattern. Additionally, interlayer conductivity is achieved through metallized vias, so the PCB manufacturing process also involves drilling and metallization plating to enable interlayer connections.
Taking a standard six-layer PCB as an example, the manufacturing process is as follows:
1. First, Produce Two Double-Sided Boards Without Holes
- Cutting: Start with raw double-sided copper-clad laminate.
- Inner Layer Pattern Creation: Form the resist pattern on the inner layers.
- Inner Layer Etching: Remove excess copper foil through etching.
2. Laminate the Two Prepared Inner Layer Core Boards with Epoxy Resin and Fiberglass Prepreg
The two inner layer core boards are aligned with prepreg and laminated. Copper foil is placed on both outer layers, and the stack is pressed under high temperature and pressure to bond the layers together. The key material is the prepreg, which has the same composition as the raw material (epoxy resin and fiberglass) but is in a semi-cured state. At 70-80°C, it liquefies, and at 150°C, it undergoes a cross-linking reaction with the resin to fully cure, becoming irreversible. This transformation from semi-solid to liquid to solid, under high pressure, ensures strong bonding.
Prototyping Challenges in Multilayer PCBs
Multilayer PCBs are more complex than single or double-layer boards, both in design and manufacturing. Care must be taken to avoid certain challenges during prototyping. Below are some key difficulties in multilayer impedance board prototyping:
1. Interlayer Alignment Challenges
Due to the high number of layers in multilayer PCBs, alignment accuracy between layers has become increasingly critical. Typically, the alignment tolerance between layers is controlled within 75 micrometers. Factors such as large unit sizes, variations in temperature and humidity in the graphic conversion workshop, misalignment caused by inconsistencies between core boards, and interlayer positioning methods make alignment control even more challenging.
2. Internal Circuit Fabrication Challenges
Multilayer PCBs often use special materials such as high-TG, high-speed, high-frequency, thick-copper, and thin-dielectric layers, which impose high demands on internal circuit fabrication and dimensional control. For example:
- Impedance requirements for signal integrity increase the difficulty of internal circuit fabrication.
- Smaller line widths and spacing increase the likelihood of open and short circuits, reducing yield.
- Multiple fine-line signal layers increase the probability of AOI (Automated Optical Inspection) missing defects.
- Thin inner core boards are prone to wrinkling, poor exposure, and curling during etching.
- High-layer-count boards are often system boards with large unit sizes, making product scrap costs high.
3. Lamination Challenges
The stacking of multiple inner core boards and prepreg layers can lead to defects such as layer slippage, delamination, resin voids, and trapped air bubbles. The lamination structure design must consider material properties such as heat resistance, pressure resistance, resin content, and dielectric thickness to develop a reasonable lamination plan. Additionally, controlling expansion and contraction and compensating for dimensional factors become more difficult with higher layer counts, and thin interlayer insulation can lead to reliability test failures.
4. Drilling Challenges
The use of special materials like high-TG, high-speed, high-frequency, and thick-copper boards increases the difficulty of achieving smooth drill holes, removing burrs, and cleaning drill residues. Challenges include:
- High total copper thickness and board thickness increase the risk of drill breakage.
- Dense BGA (Ball Grid Array) layouts with narrow hole-to-hole spacing can lead to CAF (Conductive Anodic Filament) failures.
- Thick boards are prone to drill wander, resulting in angled holes.
By addressing these challenges, manufacturers can improve the quality and reliability of multilayer PCB prototypes, ensuring they meet the stringent requirements of modern electronic designs.