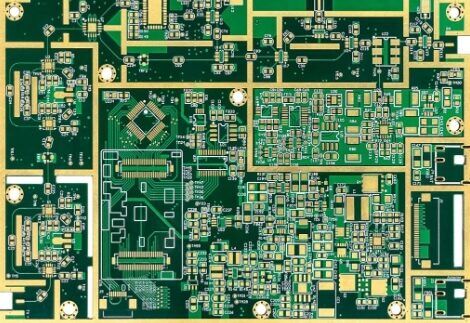
Preface
Designing multilayer PCBs demands precision, thorough planning, and a deep understanding of both physical principles and manufacturing constraints. In this article, we delve into the multilayer PCB design guidelines that every engineer should follow to avoid common pitfalls. Through detailed analysis, data visualizations, and interactive elements, you’ll gain insights into the micro-structural differences that can make or break your design.
Introduction
Multilayer PCBs are the backbone of complex electronic systems—from high-frequency RF circuits to advanced automotive and medical electronics. However, without adherence to proper multilayer PCB design guidelines, even a minor error can lead to issues such as signal integrity degradation, EMI interference, or thermal imbalances. In this article, we explore the top 10 design mistakes, explain the underlying physics, and offer actionable tips to improve your design process.
Advanced layout engineer’s professional tip: Always integrate design rules early in your development phase to avoid costly iterations later on.
1. Inadequate Layer Stack-Up Planning
Mistake: Failing to optimize the layer arrangement can lead to poor impedance control and increased crosstalk.
Physical Principle: The layer stack-up influences the electromagnetic field distribution. An improper stack-up can disrupt the controlled impedance, based on transmission line theory.
Guidelines:
- Use simulation tools to model electromagnetic behavior.
- Follow established multilayer PCB design guidelines for impedance matching.
- Maintain balanced signal layers with adjacent ground or power planes.
Data Visualization:
A diagram illustrating different stack-up configurations and their corresponding impedance profiles helps visualize how layer arrangement affects signal propagation.
2. Poor Signal Integrity Due to Impedance Mismatch
Mistake: Overlooking the importance of controlled impedance in high-speed circuits.
Physical Principle: Transmission line theory dictates that the trace geometry, dielectric constant, and distance from the reference plane determine impedance. Mismatches lead to reflections and signal loss.
Guidelines:
- Calculate impedance using precise formulas or simulation software.
- Adjust trace width, spacing, and dielectric properties to achieve target impedance values.
3. Insufficient Via Management
Mistake: Overusing or misplacing vias can cause increased inductance and impedance discontinuities.
Physical Principle: Vias act as vertical interconnects, but each via introduces parasitic inductance and capacitance that affect high-speed signals.
Guidelines:
- Minimize the number of vias in critical signal paths.
- Use back-drilling techniques to remove unused via stubs.
- Ensure via dimensions comply with design standards.
Industry Case:
In automotive control systems, precise via management has proven essential for maintaining signal integrity in densely routed PCBs. Read more.
4. Neglecting Thermal Management
Mistake: Overlooking the importance of heat dissipation in multilayer designs.
Physical Principle: Thermal conductivity and heat spreading depend on material selection and board design. Poor thermal management can lead to hotspots and reliability issues.
Guidelines:
- Incorporate thermal vias and heat sinks where needed.
- Utilize thermal simulation tools to predict temperature distribution across layers.
- Choose high-Tg materials for boards operating at elevated temperatures.
Data Visualization:
A thermal map simulation showing temperature gradients across a multilayer PCB enhances understanding of heat dissipation challenges.
5. Inadequate Grounding and Power Plane Design
Mistake: Poorly designed ground and power planes lead to increased EMI and power noise.
Physical Principle: The uniformity of the reference plane affects return currents and electromagnetic interference. Discontinuities in the ground plane can lead to radiated emissions.
Guidelines:
- Design continuous, unbroken ground planes.
- Use stitching vias to connect layers and improve return paths.
- Follow multilayer PCB design guidelines for optimal power distribution.
6. Overlooking Differential Pair Routing
Mistake: Incorrect routing of differential pairs causes signal skew and impedance imbalance.
Physical Principle: Differential signaling relies on matched impedance and equal trace lengths to minimize noise and maximize signal integrity.
Guidelines:
- Maintain consistent spacing and routing lengths.
- Use simulation tools to validate differential impedance.
- Avoid sharp bends and sudden width changes.
7. Failing to Conduct Rigorous Design Rule Checks (DRC)
Mistake: Relying solely on manual inspection rather than automated design rule checking.
Physical Principle: In multilayer designs, minor deviations can accumulate, affecting performance and reliability. Automated DRC ensures adherence to engineering standards.
Guidelines:
- Implement comprehensive DRCs using advanced EDA tools.
- Cross-check parameters like trace width, spacing, and via dimensions with international standards.
8. Underestimating Material Selection Impact
Mistake: Using inappropriate materials without considering dielectric properties and thermal performance.
Physical Principle: The choice of substrate (e.g., FR4, Rogers, PTFE) affects the dielectric constant, signal loss, and overall board performance. The physical properties of the material directly influence signal propagation.
Guidelines:
- Select materials based on frequency requirements and operating conditions.
- Verify material specifications with test data and simulation results.
- Balance cost with performance demands.
Industry Case:
Medical electronics often demand PTFE-based laminates for their superior signal integrity, especially in high-frequency applications.
9. Ignoring the Impact of Crosstalk and Electromagnetic Interference (EMI)
Mistake: Failing to mitigate crosstalk between adjacent traces can lead to data corruption.
Physical Principle: Crosstalk is caused by capacitive and inductive coupling between traces. Understanding the physical interactions helps in minimizing interference.
Guidelines:
- Increase trace spacing and introduce ground guard traces between high-speed lines.
- Use differential routing where possible.
- Employ simulation software to predict EMI issues.
10. Lack of Collaboration Between Design and Manufacturing
Mistake: Not involving the manufacturing team early in the design process can lead to misinterpretations and costly rework.
Physical Principle: The feasibility of a design is closely tied to the manufacturing process. Communication gaps can result in non-manufacturable designs, affecting yield and reliability.
Guidelines:
- Establish early and continuous communication with your manufacturer.
- Use design for manufacturability (DFM) tools and follow standardized multilayer PCB design guidelines.
- Regularly review design changes with production engineers.
Transition Note: Each design mistake often has cascading effects on overall performance. A holistic approach, combining robust simulation, early prototyping, and iterative testing, can significantly reduce errors.
Glossary Sidebar
- Impedance Control: The process of maintaining a specific resistance to the flow of electrical current along a PCB trace.
- Differential Pair: A pair of traces designed to carry equal and opposite signals, reducing noise and EMI.
- DRC (Design Rule Check): Automated verification of design parameters against industry and manufacturer standards.
- Crosstalk: Unwanted interference caused by electromagnetic coupling between adjacent PCB traces.
- Thermal Via: A via designed to conduct heat from one layer to another, enhancing thermal dissipation.
Frequently Asked Questions (FAQ)
Q1: What are multilayer PCB design guidelines?
A: These are comprehensive rules and best practices covering layer stack-up, impedance control, via management, and material selection to ensure optimal performance and manufacturability.
Q2: How does layer stack-up affect impedance control?
A: The arrangement of signal and reference planes in the stack-up determines the electromagnetic field distribution, which in turn affects the controlled impedance required for high-speed circuits.
Q3: Why is differential pair routing critical in multilayer designs?
A: Differential pairs minimize noise and EMI by ensuring matched impedance and equal path lengths, which are essential for maintaining signal integrity in high-frequency applications.
Conclusion
Avoiding these top 10 design mistakes is vital for developing reliable, high-performance multilayer PCBs. By adhering to proven multilayer PCB design guidelines, leveraging simulation and DRC tools, and fostering close collaboration between design and manufacturing teams, you can enhance signal integrity, minimize EMI, and ensure overall design robustness.
For additional insights, refer to the IEEE Research on Multilayer PCB Technologies and industry-standard documents like IPC-6012. Adopting a proactive, data-driven design approach will not only improve your design quality but also lead to significant cost savings in the long run.
Remember, every design iteration is an opportunity to learn and refine your process. Keep testing, stay updated with industry standards, and continuously improve your design practices.