The via design in high multilayer PCB boards is a critical step that directly impacts electrical performance and reliability.
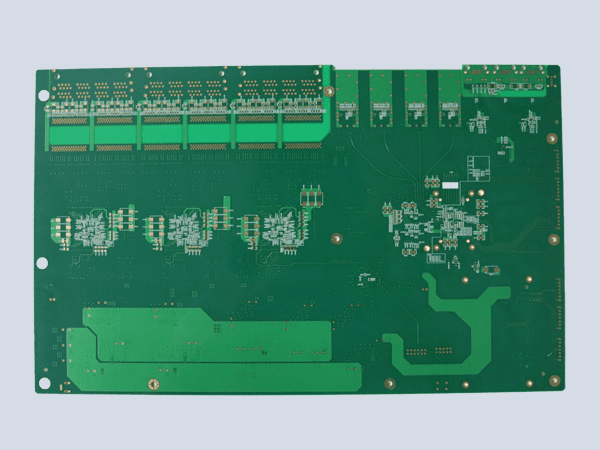
1. Via Types
- Through-Hole Via: Passes through all layers, suitable for simple designs but occupies more space.
- Blind Via: Connects the outer layer to an inner layer without passing through the entire board, saving space.
- Buried Via: Connects only between inner layers and does not reach the outer layers, suitable for high-density designs.
2. Via Dimensions
- Hole Size: Determined based on current and signal requirements, typically ranging from 0.2mm to 0.5mm.
- Pad Diameter: Should be 0.2mm to 0.4mm larger than the hole size to ensure reliable connections.
3. Via Placement
- Signal Integrity: High-speed signal vias should be placed close to the signal path to minimize reflections and losses.
- Power and Ground: Power and ground vias should be placed near relevant components to reduce impedance.
4. Via Filling
- Conductive Filling: Used for high-current or thermal dissipation requirements, such as copper filling.
- Non-Conductive Filling: Used for ordinary signal vias, such as resin filling.
5. Via Layout
- Uniform Distribution: Avoid clustering vias to prevent mechanical stress concentration.
- Avoid Sensitive Areas: Keep vias away from high-frequency signal lines and antenna regions.
6. Via and Interlayer Connections
- Layer Alignment: Ensure vias are aligned across layers to avoid misalignment.
- Impedance Matching: High-speed signal vias require impedance matching to reduce signal reflections.
7. Manufacturing Processes
- Laser Drilling: Used for micro vias, such as blind and buried vias.
- Mechanical Drilling: Used for larger vias, such as through-hole vias.
8. Simulation and Testing
- Signal Integrity Simulation: Ensures via design does not affect signal quality.
- Thermal Simulation: Evaluates the impact of vias on thermal dissipation.
- Electrical Testing: Verifies the electrical connectivity and reliability of vias.
From a design perspective, a via primarily consists of two parts: the central drill hole and the pad area surrounding the hole. The dimensions of these two parts determine the size of the via. Clearly, in high-speed, high-density PCB design, designers always prefer smaller vias, as this allows more routing space on the board. Additionally, smaller vias have lower parasitic capacitance, making them more suitable for high-speed circuits. However, reducing the via size also increases costs, and the size of vias cannot be minimized indefinitely due to limitations in drilling and plating technologies. The smaller the hole, the longer it takes to drill, and the more likely it is to deviate from the center. Moreover, when the depth of the hole exceeds six times its diameter, it becomes impossible to ensure uniform copper plating on the hole walls. For example, if a standard 6-layer PCB has a thickness (through-hole depth) of 50 mils, the minimum drill diameter that PCB manufacturers can typically provide is 8 mils.
With the advancement of laser drilling technology, the size of drilled holes can now be made increasingly smaller. Generally, vias with diameters of 6 mils or less are referred to as microvias. Microvias are frequently used in HDI (High-Density Interconnect) designs. Microvia technology allows vias to be placed directly on pads (Via-in-pad), which significantly enhances circuit performance and saves routing space.
Summary
The via design in high multilayer PCBs requires comprehensive consideration of signal integrity, power integrity, thermal management, and manufacturing processes. Through rational design and simulation testing, performance and reliability can be ensured.