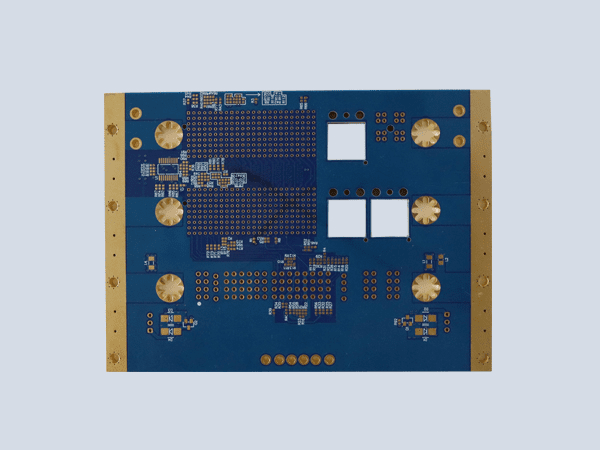
Causes
- Material Issues
- Moisture Absorption: PCB materials (e.g., FR-4) absorb moisture during storage or processing, leading to delamination and blistering when heated.
- Poor Material Quality: Substandard base materials or prepreg with insufficient bonding strength or uneven resin content.
2. Process Issues
- Improper Lamination: Insufficient temperature, pressure, or time during lamination, resulting in weak interlayer bonding.
- Uneven Lamination: Non-uniform pressure distribution during lamination, causing poor bonding in localized areas.
- Inadequate Cleaning: Residual contaminants on surfaces before lamination affect bonding.
3. Design Issues
- Uneven Copper Distribution: Uneven copper foil distribution leads to significant differences in the coefficient of thermal expansion (CTE) in localized areas.
- Poor Via Design: Dense via areas are prone to stress concentration, causing delamination.
4. Environmental Factors
- High Humidity: High humidity in the production environment causes material moisture absorption.
- Temperature Variations: Extreme temperature changes cause material expansion or contraction, generating stress.
Solutions
- Material Control
- Use High-Quality Materials: Select high-quality base materials and prepreg with proper resin content and bonding strength.
- Moisture Prevention: Store materials in a dry environment and pre-bake to remove moisture (e.g., 120°C for 2-4 hours) before use.
2. Process Optimization
- Control Lamination Parameters: Ensure proper temperature, pressure, and time during lamination to avoid excessive heat or insufficient pressure.
- Uniform Lamination: Ensure even pressure distribution during lamination to prevent poor bonding in localized areas.
- Thorough Cleaning: Clean surfaces thoroughly before lamination to remove oil, dust, and other contaminants.
3. Design Improvements
- Optimize Copper Distribution: Design for even copper foil distribution to minimize localized CTE differences.
- Reasonable Via Design: Avoid dense via arrangements to reduce stress concentration.
4. Environmental Control
- Humidity Control: Maintain production environment humidity within a reasonable range (typically 40%-60%).
- Avoid Extreme Temperatures: Prevent PCBs from operating or being stored under extreme temperature conditions.
5. Testing and Monitoring
- Delamination Testing: Use ultrasonic scanning (SAT) or X-ray inspection to detect delamination issues.
- Process Monitoring: Monitor lamination parameters and environmental conditions in real-time during production to ensure process stability.
Summary
Delamination and blistering in multilayer PCBs are primarily caused by material, process, design, and environmental factors. By selecting high-quality materials, optimizing process parameters, improving designs, and controlling environmental conditions, delamination issues can be effectively resolved, enhancing the reliability and quality of PCBs.