The production process of rigid-flex PCBs is as follows:
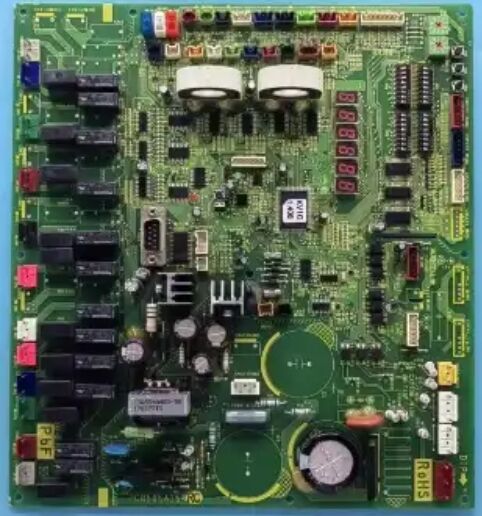
01 Design Board Acceptance
The factory’s engineering department receives and inspects the design board files sent by the customer.
The inspection includes:
- Whether the design files are appropriate.
- Whether any layers are missing.
- Ensuring the files have borders.
- Verifying the existence of drilling files.
If there are design defects, the engineering department will notify the designer to make corrections. If there are no design issues, mass production can proceed according to the design.
02 Printing the Design onto Transparent Film
The inspected design files are printed onto transparent film.
Light is projected onto these films to expose the photoresist on the circuit board, similar to exposing a photograph. The circuit board design comes to life on the film, vivid and dynamic.
03 Cutting and Edge Grinding of Fiberglass
Fiberglass is selected, cut, and ground.
FR-4 type fiberglass with copper-clad top and bottom layers is chosen and cut to the designed dimensions using a cutting machine. Since the edges of the fiberglass are too rough, they are polished.
04 Inner Layer Production
The top and bottom layers of the fiberglass are covered with a plastic dry film and hardened under ultraviolet light.
After both sides of the fiberglass are hardened with dry film, they are pressed together using a machine. This effectively prevents the copper from being dissolved by alkaline solutions in subsequent processes.
05 Etching Process
The purpose of the entire etching process is to remove excess copper and photoresist from the copper board, completing the prototype of the PCB through a series of steps.
Excess copper and photoresist on the laminated fiberglass are removed by immersion in an alkaline solution. The etching process is completed through stripping, rinsing, drying, and dry film lamination.
06 Automatic Optical Inspection (AOI) and Vacuum Lamination (PP)
The purpose of Automatic Optical Inspection (AOI) is to check the etching of the inner layers, ensuring all inner layer etching is correct.
Vacuum lamination involves attaching yellow epoxy-like patches to the sides of the board to increase adhesion.