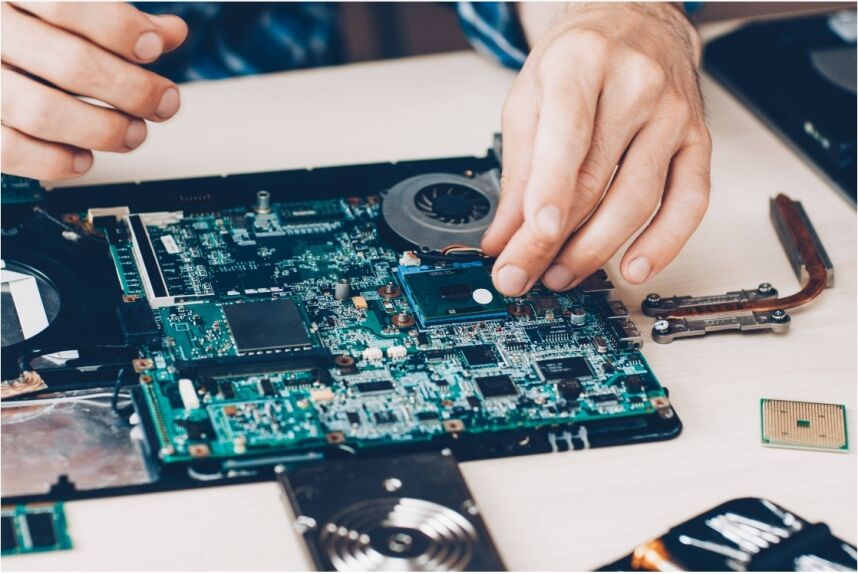
Introduction
Selecting the right PCB assembly services is crucial to ensuring the performance, reliability, and cost-effectiveness of your electronic product. Whether you’re developing high-frequency RF circuits, automotive control systems, or medical-grade PCBs, choosing the wrong service provider can lead to production delays, quality issues, and increased costs. This guide provides a detailed breakdown of key factors to consider, backed by engineering principles, industry applications, and technical data.
1. Understanding PCB Assembly Services
1.1 What is PCB Assembly?
PCB Assembly (PCBA) is the process of mounting electronic components onto a bare PCB through techniques such as Surface Mount Technology (SMT) and Through-Hole Technology (THT).
Assembly Type | Description | Application |
---|---|---|
SMT (Surface Mount Technology) | Soldering small components directly onto PCB pads | High-density designs, consumer electronics |
THT (Through-Hole Technology) | Components inserted through PCB holes and soldered on the opposite side | Power electronics, aerospace applications |
Mixed Assembly | Combination of SMT and THT for complex designs | Industrial automation, IoT devices |
1.2 Key Factors Affecting PCB Assembly Quality
- Component Placement Accuracy: Modern SMT lines achieve ±25 μm placement precision, critical for fine-pitch BGAs.
- Solder Paste Application: Stencil aperture design directly impacts solder volume and joint quality.
- Reflow Profile Control: Prevents defects like cold joints and voiding in BGA solder balls.
2. Key Criteria for Selecting a PCB Assembly Service
2.1 Manufacturing Capabilities
The complexity of your PCB dictates the required manufacturing capabilities. Consider:
- Minimum Trace/Space: 3 mil (0.075 mm) or lower for high-density designs.
- Microvia Technology: Essential for HDI PCBs with stacked vias.
- Solder Mask & Surface Finish Options: ENIG, HASL, OSP for different environments.
2.2 Quality Control & Testing Standards
Reliable PCB assembly services should offer comprehensive testing:
- Automated Optical Inspection (AOI): Detects missing components and misalignments.
- X-ray Inspection: Required for BGAs, CSPs, and hidden joints.
- In-Circuit Testing (ICT): Ensures circuit integrity before final assembly.
2.3 Turnaround Time & Scalability
Fast prototyping services (24-48 hours) vs. mass production lead times (4-6 weeks).
- Batch Size Considerations: Small-batch prototyping vs. large-scale production.
- Supply Chain Management: Component sourcing strategies to avoid shortages.
2.4 Cost vs. Quality Trade-Offs
Cost Factor | Impact on Quality |
Low-cost assembly | Risk of cold solder joints, misaligned components |
Premium-quality assembly | Higher reliability, compliance with IPC standards |
3. Industry Applications & Case Studies
3.1 High-Reliability Aerospace & Automotive PCBs
- Aerospace: PCBs must withstand -55°C to +125°C temperature variations.
- Automotive: Heavy copper PCBs for power distribution systems.
3.2 Medical & IoT Device PCB Assembly
- Medical PCBs: Require ISO 13485-certified assembly services.
- IoT Devices: Must support high-frequency RF signal integrity.
4. Ensuring Compliance with Industry Standards
4.1 IPC Classifications for PCB Assembly
- IPC Class 1: Consumer electronics (basic performance).
- IPC Class 2: Industrial and automotive electronics (higher reliability).
- IPC Class 3: Aerospace, medical, and military applications (strict quality control).
4.2 Environmental & RoHS Compliance
Ensure compliance with RoHS (Restriction of Hazardous Substances) for lead-free assembly.
5. Interactive Tools & Decision-Making Framework
5.1 How to Compare PCB Assembly Providers
Use the following checklist to evaluate PCB assembly services:
✅ Does the provider support fine-pitch BGA assembly (<0.4 mm pitch)?
✅ What quality certifications do they hold (ISO 9001, ISO 13485)?
✅ Do they offer functional testing and X-ray inspection?
✅ Can they handle flexible PCB assembly for IoT applications?
Conclusion
Choosing the right PCB assembly services requires a careful evaluation of technical capabilities, quality standards, and production scalability. Whether you’re developing high-frequency RF circuits, medical electronics, or industrial automation systems, a well-selected assembly partner ensures long-term reliability and efficiency.
Glossary of Key Terms
- BGA (Ball Grid Array) – A high-density component packaging method.
- HDI (High-Density Interconnect) – Advanced PCB technology for compact designs.
- ENIG (Electroless Nickel Immersion Gold) – A reliable PCB surface finish.
References & External Resources
- IPC-6012B Standard for PCB Fabrication
- IEEE Research on High-Frequency PCB Signal Integrity