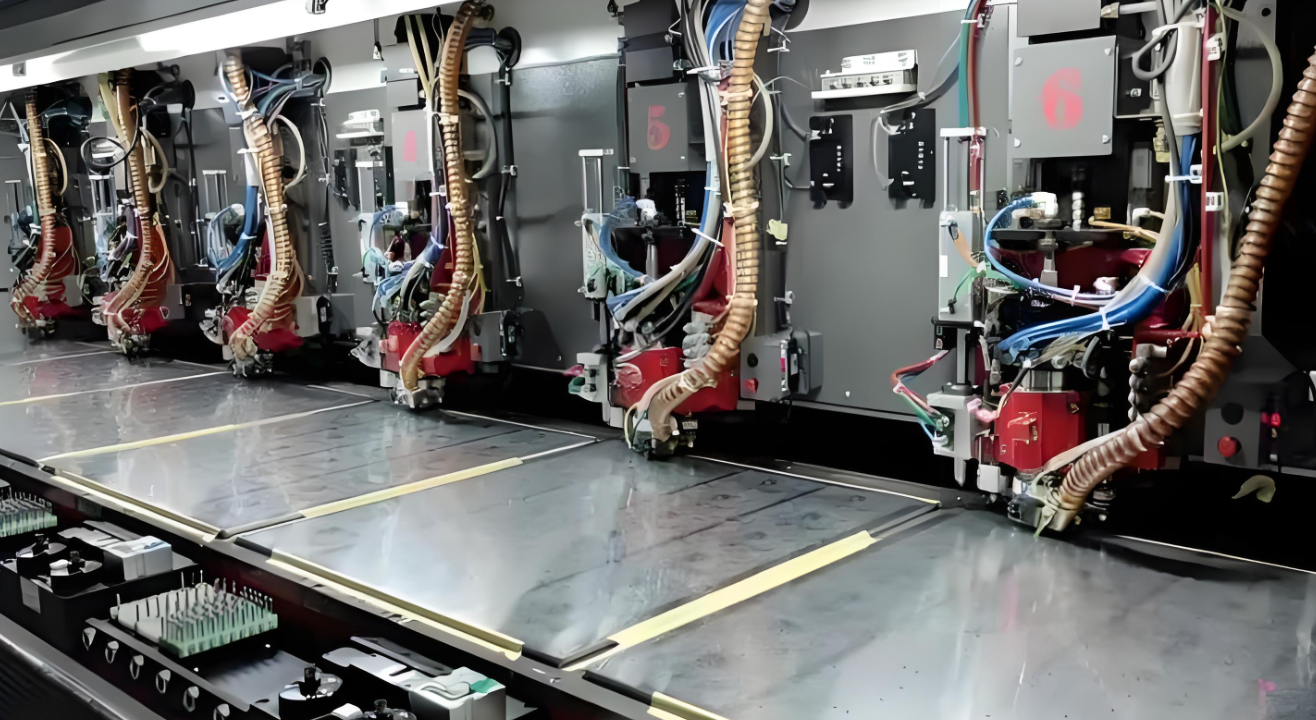
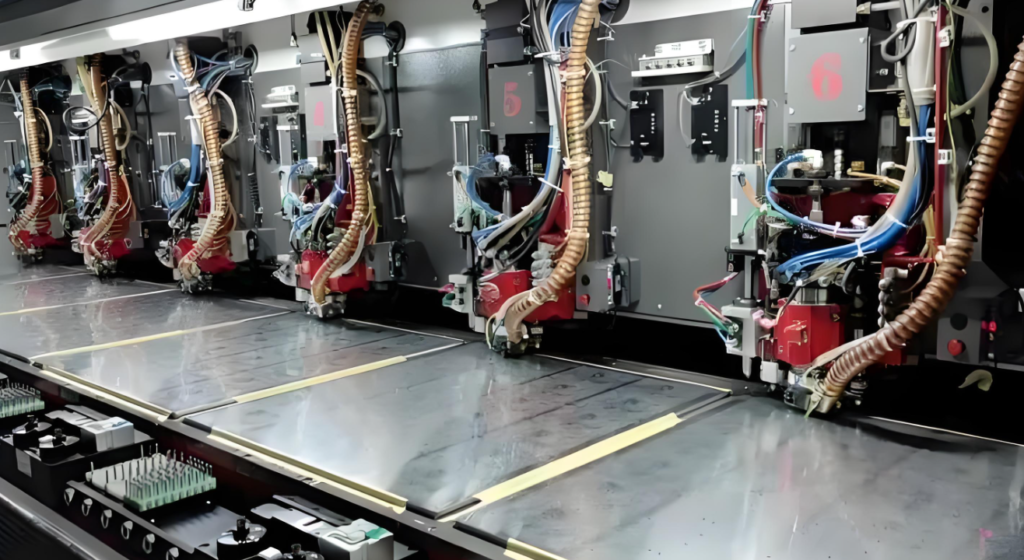
In the complex process of printed circuit board manufacturing, the PCB drilling process undoubtedly plays a pivotal role, which profoundly affects the electrical connection performance of the PCB, the installation effect of components and the overall functional performance. Accurate and efficient drilling operations are the key to giving PCBs strong vitality and ensuring the stable operation of electronic equipment.
1.The core points of PCB drilling technology
(I) The accuracy of drill bit selection
The drill bit, as the core tool of the drilling process, is very important. First, the drill bit material needs to be carefully selected according to the material characteristics of the PCB. Carbide drill bits are widely used in a variety of PCB substrate materials such as FR-4 boards and metal-based boards due to their high hardness and excellent wear resistance. For special materials such as flexible PCBs or ceramic-based PCBs, drill bits with special toughness or cutting performance need to be selected. Secondly, the diameter specifications of the drill bit must be precisely matched with the PCB design requirements. From tiny microholes for fine chip-level connections to large-diameter holes for installing plug-in components, each drill bit must perform its duties to ensure that each hole can meet the stringent requirements of circuit layout and component assembly.
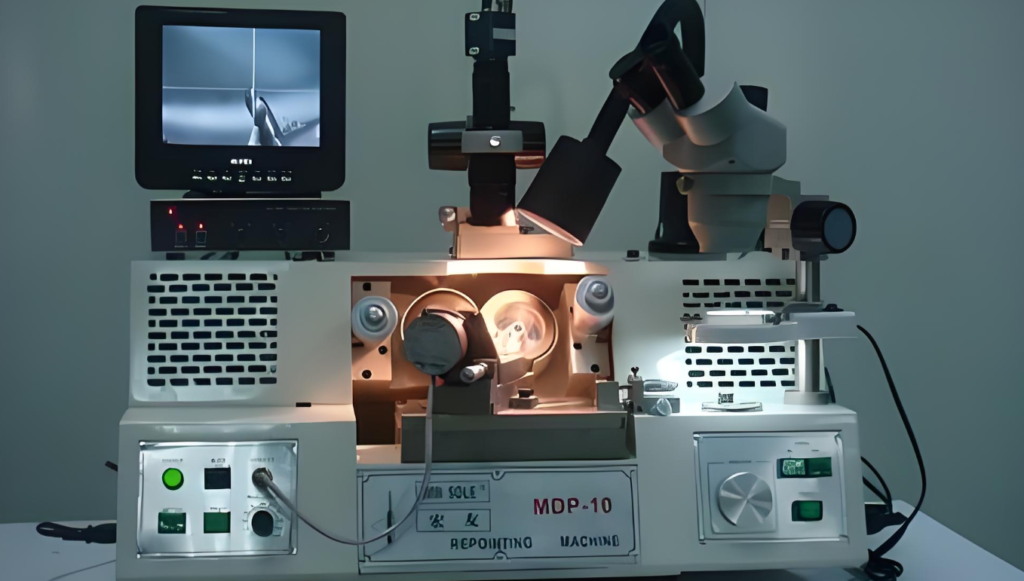
(II) Accurate setting of drilling parameters
Drilling parameters, including rotation speed and feed speed, have a direct and far-reaching impact on drilling quality. If the rotation speed is too high, the wear of the drill bit will increase, which may cause overheating, resulting in scorching and delamination of the PCB substrate; if the rotation speed is too low, the drilling efficiency will be low, and poor chip breaking will occur, which will affect the quality of the hole wall. The feed speed and the rotation speed need to be adjusted in coordination. If the feed speed is too fast, the drill bit will be subjected to excessive force, resulting in rough hole walls, hole diameter deviation and even drill bit breakage; if the feed speed is too slow, it will reduce production efficiency and increase unnecessary costs. Therefore, when drilling ordinary FR-4 boards, the rotation speed needs to be controlled within a reasonable range, and the feed speed needs to be reasonably set according to the drill bit diameter to ensure that the drilled hole wall is smooth and the hole diameter is uniform.
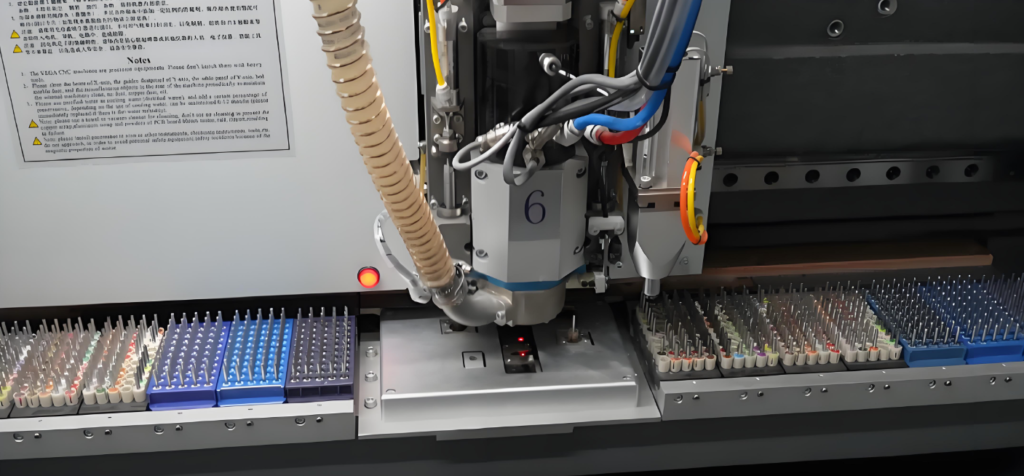
(III) Strict control of positioning accuracy
Before drilling, it is crucial to ensure the accurate positioning of the PCB board on the drilling equipment. Usually, a precision fixture or vacuum adsorption device is used to fix the PCB to prevent the board from shifting during the drilling process. For multi-layer PCBs, due to the extremely high alignment accuracy requirements between layers, a high-precision optical positioning system or mechanical positioning pins are also required to ensure that the drilling positions of each layer are completely overlapped, thereby avoiding misalignment between layers and ensuring the reliability of electrical connections. Once the positioning is deviated, the components installed subsequently will not be able to accurately connect to the corresponding circuit layer, which will lead to PCB failure.
(IV) Efficiency of chip removal
A large amount of chips will be generated during the drilling process. If they are not handled in time, a series of problems will occur. The accumulated chips may scratch the hole wall, increase the roughness of the hole wall, and affect the electroplating effect; they may also block the chip removal groove of the drill bit, resulting in poor heat dissipation of the drill bit, accelerating the wear of the drill bit or even breaking it. To solve this problem, on the one hand, the chip removal groove structure needs to be optimized in the drill bit design to make it more conducive to the discharge of chips; on the other hand, an air blowing or dust suction device can be used to assist in chip removal. When drilling, blow air into the hole to blow the chips out of the hole, or use a dust suction device to suck the chips away in time to keep the drilling area clean.
2.Effective methods to ensure drilling accuracy
(I) Use high-precision drilling equipment
Advanced CNC drilling machines provide a solid guarantee for drilling accuracy. These devices are equipped with high-precision spindles, ball screw transmission systems and precision control systems, which can accurately control the movement trajectory, rotation speed and feed speed of the drill bit. For example, the positioning accuracy of some high-end CNC drilling machines can reach micron level. When drilling holes with small apertures, the aperture deviation can still be controlled within a very small range, thus meeting the stringent requirements of high-end PCBs such as chip carriers and high-speed communication PCBs for drilling accuracy.
(II) Regularly calibrate and maintain equipment
The accuracy of the equipment is the basis for ensuring the quality of drilling. Even the most advanced equipment will gradually decrease in accuracy if it lacks regular calibration and maintenance. Therefore, it is necessary to regularly check and calibrate key components such as the spindle accuracy, table flatness, and positioning system of the drilling equipment. At the same time, regularly replace worn transmission components such as ball screws, guide rails, etc. to ensure the accuracy of equipment movement. In addition, the control system of the equipment needs to be upgraded with software, the algorithm needs to be optimized, and the control accuracy of the drilling process needs to be improved so that the equipment is always in the best working state.
(III) Optimizing the drilling process route
Reasonable planning of the drilling sequence is also crucial to improving drilling accuracy. For multi-layer PCBs, small holes should be drilled first and then large holes to reduce the stress impact on the drilled small hole area when drilling large holes and avoid deformation of small holes. When drilling holes in different areas, the principles of symmetry and uniformity should be followed as much as possible to avoid deformation of the PCB board due to uneven force caused by unreasonable drilling sequence, which in turn affects the drilling accuracy. In addition, the drilling process route can be simulated and optimized with simulation software to discover potential accuracy problems in advance and adjust them, which can greatly improve the success rate of actual operations.
(IV) Strengthening the quality inspection link
After the drilling is completed, timely and strict quality inspection is indispensable. High-precision measuring tools, such as electronic calipers and two-dimensional image measuring instruments, are required to measure key indicators such as hole diameter, hole position accuracy, and hole wall roughness. For multi-layer PCBs, it is also necessary to check the inter-layer alignment through X-ray detection equipment to ensure that there is no misalignment or short circuit between layers. Once a quality problem is found, the cause must be traced immediately, and the drilling process parameters, equipment status, etc. must be adjusted and corrected to prevent unqualified products from flowing into the next process.
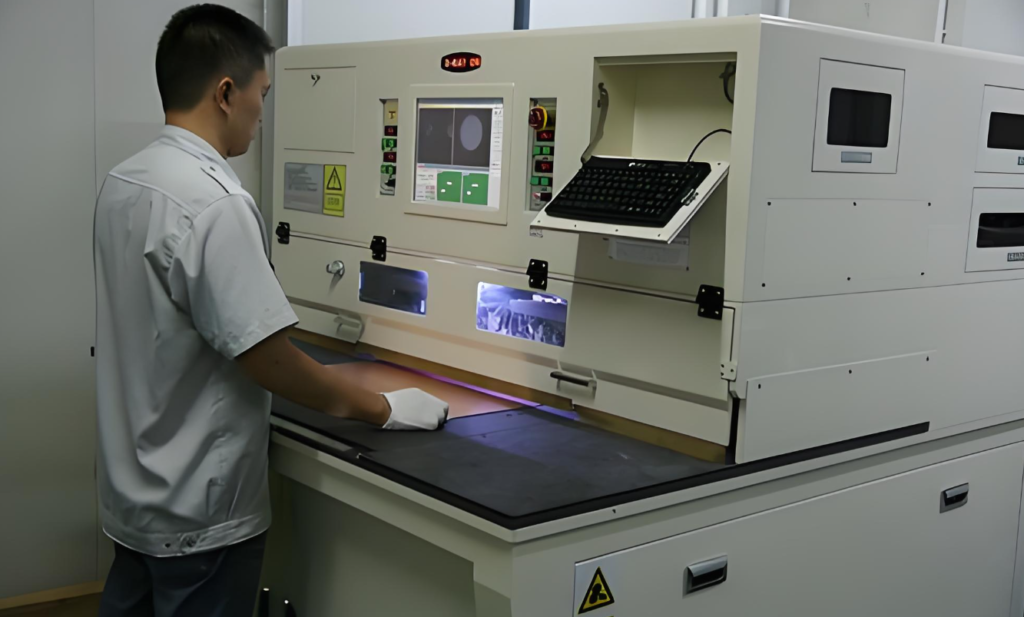
Hongxin Circuit Co., Ltd. has a deep technical background and rich practical experience in the field of PCB manufacturing, and has a precise grasp of the key points of the drilling process and precision assurance measures. The company is equipped with advanced CNC drilling equipment. From the fine selection of drill bits to the optimization setting of drilling parameters, to the strict control of positioning accuracy and the efficient execution of chip removal, every link is carefully controlled by a professional technical team. Relying on strong technical R&D capabilities and equipment maintenance capabilities, whether it is using high-precision equipment to ensure drilling accuracy, or regular calibration and maintenance to keep the equipment alive, or optimizing the process route and strengthening quality inspection, Hongxin Circuit Co., Ltd. can ensure the high-quality completion of the drilling process from the source to the finished product.
HXPCB Provide 1-6 layers PCB free proofing service
sales@hongxincircuit.com Whatsapp: +8618123677761 Wechat: PCBA18682318008
HXPCB is a professional printed circuit board (PCB) manufacturer. HXPCB provides flexible and fast production services (12 to 72 hours) to customers around the world, offering PCB prototyping, small to large PCB manufacturing, and PCB assembly. Its products include 2-30 layer FR-4 PCB, IMS PCB, HDI board, high-precision PCB, etc.